Seagreen - foundation installation for the world's deepest offshore wind farm
Huge buckets, silently sucked into the seabed with the opening down, keep the wind turbines on the Seagreen field off the east coast of Scotland in place on the seabed. Together with FRAMO, NGI had the task of installing the bucket foundations on the 114 jacket substructures for the wind turbines.
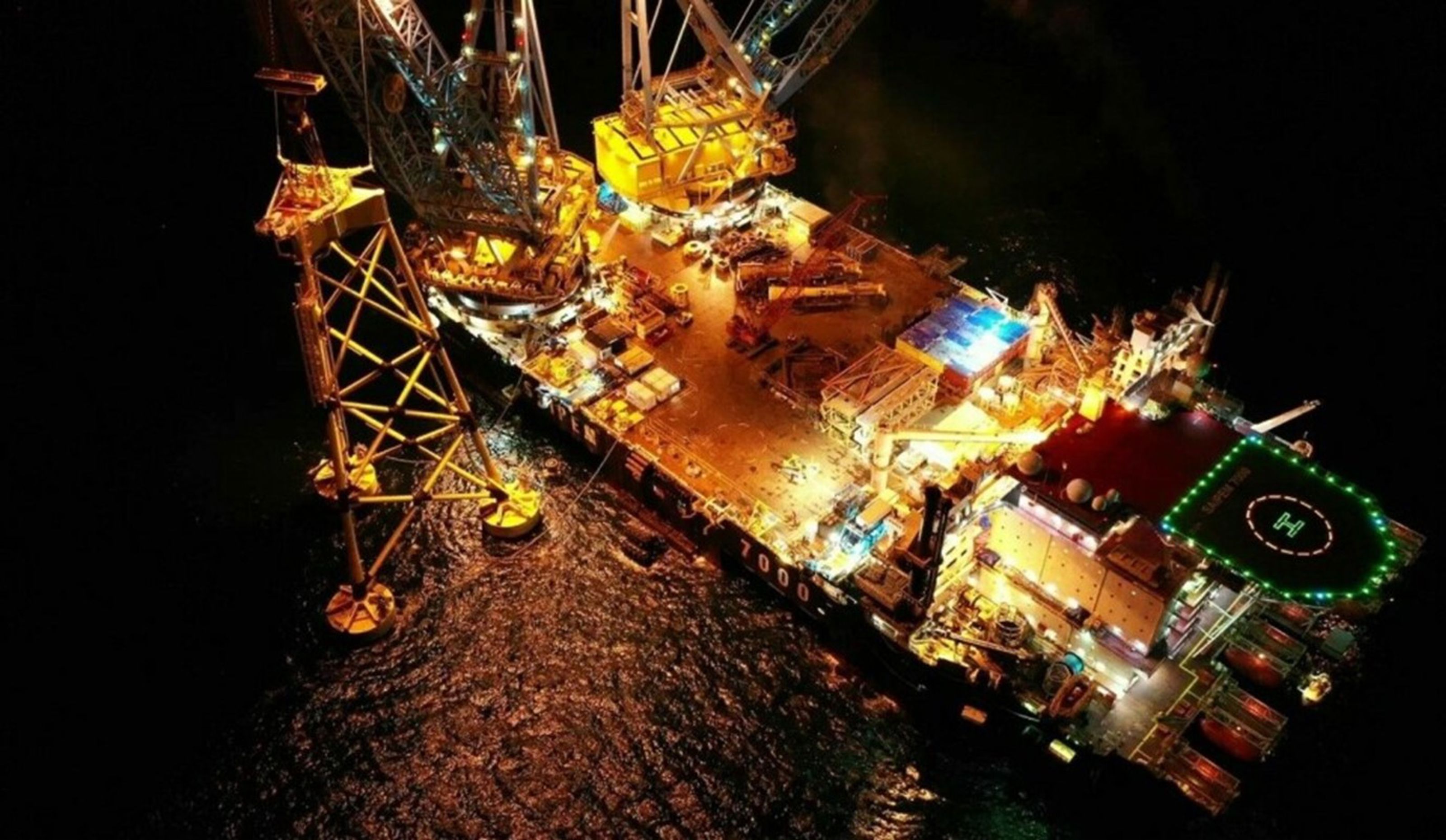
Saipem's giant crane barge S7000 was used for the transport and installation of the 114 foundation substructures at the Seagreen wind farm off the coast of Scotland ( SSE Renewables/Illustration)
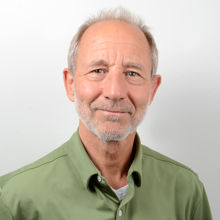
Karl Henrik Mokkelbost
Senior Specialist Field Testing and Offshore Instrumentation karl.henrik.mokkelbost@ngi.no+47 928 63 592
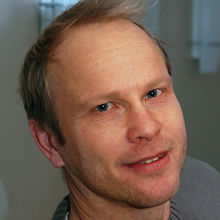
Per Sparrevik
Expert Adviser Field Testing and Offshore Instrumentation per.sparrevik@ngi.no+47 924 91 449